Welding two heavy or unwieldy workpieces together can be a simple and straightforward task done in a few minutes. That is, if you have the right gear. First, those workpieces need to be perfectly aligned so you get the weld at the correct angle. What bothers most welders is that they don’t always have that extra pair of helping hands to keep workpieces from moving, or the extra cash in getting especially expensive fixturing gear. So, what are your options?
All you need for the perfect weld is a set of welding magnets and clamps. These will let you position any type of metals, ferrous with magnets and clamps for all others, and at the desired angles for the weld. They also have high holding strength, so are good for both smaller metal pieces, or something much heavier. And they can be used in different settings and workpieces in all sorts of shapes.
What is a Welding Magnet?
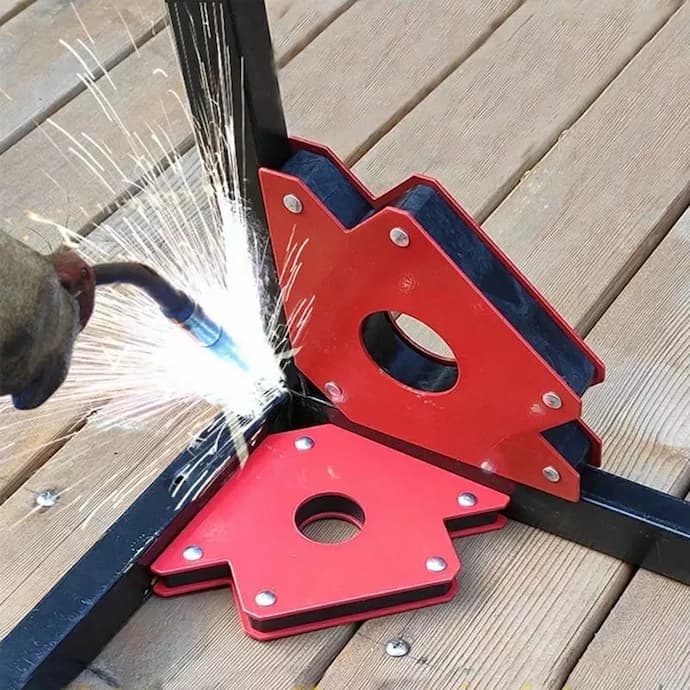
Welding magnets are the essential welding accessory. They contain strong magnets set within two metal plates and can hold flat, round or uneven ferrous metals in place. This allows welders more precision in setting up the workpieces in position, and better stability during the weld. They let welders concentrate on getting the perfect welding.
Welding magnets take different shapes and come in different sizes. They also have varying amounts of clamping or magnetic force. They can be combined with other magnets in more complex applications and when the weight of the workpiece becomes an issue. For tight spots, difficult angles, and where clamps are just too big or impractical, you’d want a welding magnet.
Uses of Welding Magnets
Magnets are used to lift, affix and align the metal pieces for welding. They are also useful in tack welds in larger workpieces and to hold separate pieces together during the weld. This allows work to be faster and more precise, with magnets set at the desired angles. Ferromagnetic metals, iron, nickel, cobalt and their alloys can be used with magnets. Besides welding, magnets are good for soldering and brazing applications.
Types of Magnets
There are different types of magnets used in welding:
- Arrow Magnetic Holders – these are shaped like arrowheads and allow for tight welds in smaller workpieces. They come in common angles – 45, 90 and 135 degrees so are good for inner and outer welds.
- Adjustable Magnets – when you need more flexibility and when welding at odd angles, use an adjustable welding magnet. This can either swivel the full 360° or be set within a limited range, usually between 30° and 270°. They’re good for DIY applications, pipework, welding assemblies and more.
- Multi-Angle Magnets/ Square Magnets – if you usually weld at right angles then a square magnet set at 90° works best. These come in different sizes and have some of the highest clamping force ratings, so are good in large workpieces. The same magnet has edges set at 30 and 60° and can be used for tighter inner welds.
- Corner Magnets – Need fast welds in corner assemblies and free from obstacles? Then these do a fine job. When you don’t have access to an inside joint, an L-shaped corner magnet, set at 60 or 90 degrees, Designs allow for larger workpieces, and inner sleeves are good for sheet work.
- V-Pads – the ideal magnets used in holding, positioning and welding round, flat or square workpieces in light-duty applications. Good for tack welds, pipe welds and auto panel fabrication.
- ON/OFF Magnets – Switchable magnets that can be turned on or off give welders more versatility and precision when aligning workpieces at the desired angles. Turning on the magnet secures the workpieces and you’re ready for welding. If you need to make any adjustments, simply turn the magnet off, align the pieces, and turn it on again.
Particular applications mean you’ll be using one type of welding magnet more frequently. If you need convenience, different angles, sizes and clamping force, then consider getting specialised or general-purpose magnet kits.
Welding Clamps
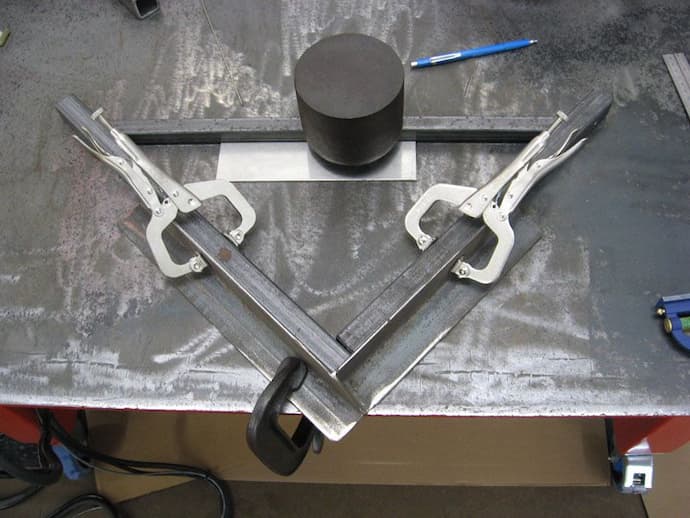
Magnets can be used separately or in combination for light and mid-duty welding applications, but sometimes don’t have the adequate clamping force. In addition, larger workpieces can be difficult to set up at the needed angles. Most welders use both magnets and clamps, and often in the same workpiece. The ultimate goal is speed and precision, and a better-looking finished product.
Types of Clamps
A wide range of general-purpose clamps are also used in welding applications. The most common are simple C or G clamps. These consist of a fixed top jaw, and a lower jaw (often padded) and are adjusted by turning a screw. They have high holding force, so offer exceptional stability, but at the expense of overall speed. Similar in design are F or Sliding clamps, which use a sliding bar to adjust the width between the two clamping jaws. They’re much faster to use and have comparable clamping force. Pipe clamps operate on the same principle, but instead of sliding bars have pipes to hold down the workpiece.
Other popular choices include Locking clamps with C-shaped jaws and a locking mechanism. These are easy to use with one hand and are commonly found in sheet metal welding. Spring clamps have spring-loaded jaws and are useful in smaller welding jobs. Quick action clamps are good for outright speed, when positioning or adjusting the workpiece, and operated by a single lever. Set squarely between magnets and clamps, are magnetic clamps. They’re typically used for larger welding and fabricating jobs as they can hold exceptionally heavy ferromagnetic pieces and can be set at 45- and 90-degree angles. You’ll find a variety of magnets and clamps in your nearest welding store.